[信息和改善准备]
在顾问师的指导下,公司成立了Kaizen改善团队。按照“教学®案例练习®实际应用”的次序,首先对团队进行了“精益系统”及改善的基础培训,并透过课堂演习与模拟,使团队成员具备了精益大师的基本技能。在此基础上首先从改善区域的信息搜集和改善准备工作入手,为现场改善工作奠定了坚实的基础。
区域信息和准备工作主要包括以下内容:
—工序流程图
—生产作业布局图
—单件循环时间、设置时间以及开机时间的分析研究
—目前工序过程中的在制品存量、生产批量、良品率以及客户定单变动系数
—目前及未来状态状态
价值流(如下图所示)
针对WIP过多,制造周期长的现状,项目团队成员通过头脑风暴以及帕累托分析等手法,初步分析了造成以上现状的主要原因:没有有效的WIP控制手段、生产批量大、设置时间长、客户需求变化较大等。
[改善过程简介]
项目展开第一天,首先用半小时召开小组会议,确定了四天工作的进度计划,以保证项目顺利完成。然后小组成员根据分工,到现场进一步搜集、核对数据,在此基础上对现状价值流进行了必要的修正,为看板系统的设计过程提供了准确的数据基础,根据进一步的原因和对策分析,确定了看板拉系统的实施范围,并确定了以下改善工作步骤:
— 看板系统的设计和计算:确定系统所需信息,计算材料补充需考虑的时间:CTI、PCT、SS以及需求变动系数,确定单张看板数量以及所需看板张数
CTI = (批量 x 良品率)/ 需求量
PCT = WIP/ 产出
— 看板卡、看板架的设计和委托制作(见附图):
— 看板运行的标准化作业程序
— 组织生产线主管和操作员进行现场模拟和试运行,观察在制品变化和材料短缺现象
— 参数的适当修正,完善看板系统
— 小组集体讨论以及多重表决,讨论确定了与拉系统相关的其它改善机会,并对其中六项主要机会制定了改善计划
跟踪改善项目:
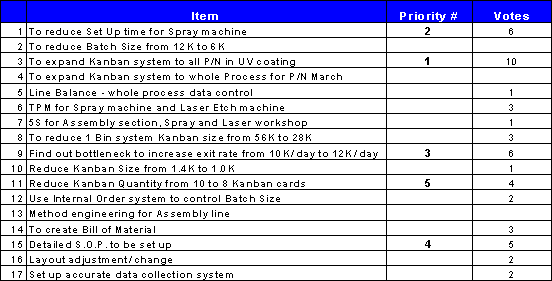
[改善效果]
透过团队改善工作的实施,UV产品库存水平降低了50%以上,制造周期时间缩短了三分之一以上,这样不仅大幅度降低了库存资金的占用,同时由于制造周期的缩短大大提高了准时发货率。
项目 现况 改善结果
MCT(天) 4.6 3.0
WIP (K) 82.2 40
如上表所列,实施看板方式以后,其它方面的相应改善将对其产生必要的支持作用,也是维护和完善拉系统的必要保证,如降低设置时间、
TPM、Poka-Yoke以及
5S等。